cnc加工工序规划是指整个工艺过程而言的,不能以某一工序的性质和某一表面的加工来判断。例如有些定位基准面,在半精加工阶段甚至在粗加工阶段中就需加工得很准确。有时为了避免尺寸链换算,在精加工阶段中,也可以安排某些次要表面的半精加工。深圳诺铂智造技术有限公司来给大家详细讲下cnc加工工艺流程吧!
1、cnc加工的零件,一般按工序集中的原则划分工序,划分的方法有以下几种:
1)按所使用刀具划分。
以同一把刀具完成的工艺过程作为一道工序,这种划分方法适用于工件的待加工表面较多的情形。加工中心常采用这种方法完成。
2)按工件安装次数划分。
以零件一次装夹能够完成的工艺过程作为一道工序。这种方法适合于加工内容不多的零件,在保证零件加工质量的前提下,一次装夹完成全部的加工内容。
3)按粗精加工划分。将粗加工中完成的那一部分工艺过程作为一道工序,将精加工中完成的那一部分工艺过程作为另一道工序。这种划分方法适用于零件有强度和硬度要求,需要进行热处理或零件精度要求较高,需要有效去除内应力,以及零件加工后变形较大,需要按粗、精加工阶段进行划分的零件加工。
4)按加工部位划分。
将完成相同型面的那一部分工艺过程作为一道工序。对于加工表面多而且比较复杂的零件,应合理安排数控加工、热处理和辅助工序的顺序,并解决好工序间的衔接问题。2.加工工序划分的原则零件是由多个表面构成的,这些表面有自己的精度要求,各表面之间也有相应的精度要求。
2、为了达到零件的设计精度要求,加工顺序安排应遵循一定的原则:
1)先粗后精的原则
各表面的加工顺序按照粗加工、半精加工、精加工和光整加工的顺序进行,目的是逐步提高零件加工表面的精度和表面质量。如果零件的全部表面均由数控机床加工,工序安排一般按粗加工、半精加工、精加工的顺序进行,即粗加工全部完成后再进行半精加工和精加工。
粗加工时可快速去除大部分加工余量,再依次精加工各个表面,这样可提高生产效率,又可保证零件的加工精度和表面粗糙度。该方法适用于位置精度要求较高的加工表面。这并不是绝对的,如对于一些尺寸精度要求较高的加工表面,考虑到零件的刚度、变形及尺寸精度等要求,也可以考虑这些加工表面分别按粗加工、半精加工、精加工的顺序完成。
对于精度要求较高的加工表面,在粗、精加工工序之间,零件最好搁置一段时间,使粗加工后的零件表面应力得到完全释放,减小零件表面的应力变形程度,这样有利于提高零件的加工精度。
2)基准面先加工原则
cnc加工一开始,总是把用作精加工基准的表面加工出来,因为定位基准的表面精确,装夹误差就小,所以任何零件的加工过程,总是先对定位基准面进行粗加工和半精加工,必要时还要进行精加工,例如,轴类零件总是对定位基准面进行粗加工和半精加工,再进行精加工。例如轴类零件总是先加工中心孔,再以中心孔面和定位孔为精基准加工孔系和其他表面。如果精基准面不止一个,则应该按照基准转换的顺序和逐步提高加工精度的原则来安排基准面的加工。
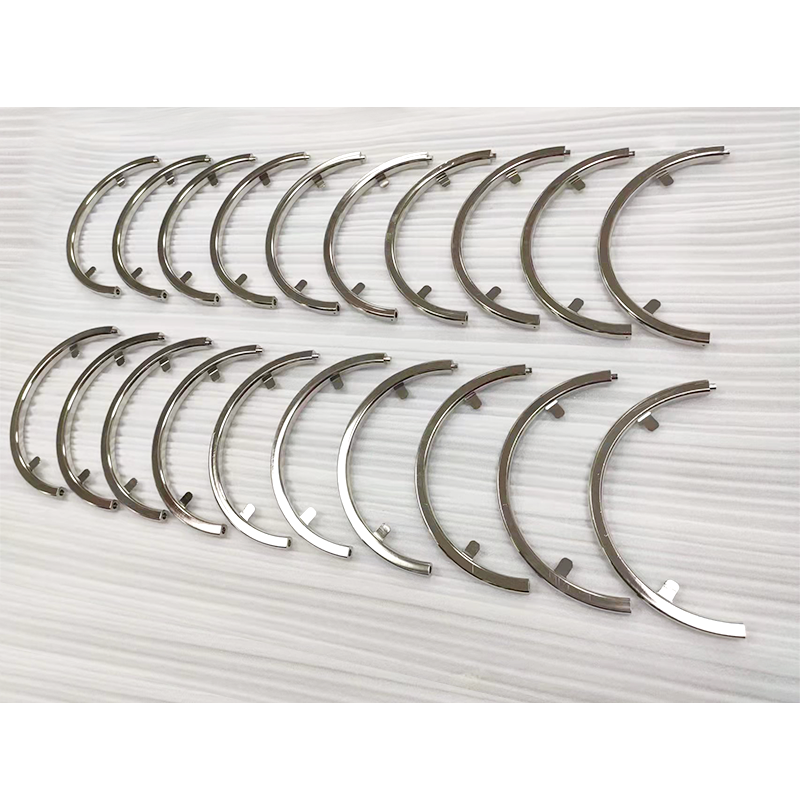
3)先面后孔原则
对于箱体类、支架类、机体类等零件,平面轮廓尺寸较大,用平面定位比较稳定可靠,故应先加工平面,后加工孔。这样,不仅使后续的加工有一个稳定可靠的平面作为定位基准面,而且在平整的表面上加工孔,加工变得容易一些,也有利于提高孔的加工精度。通常,可按零件的加工部位划分工序,一般先加工简单的几何形状,后加工复杂的几何形状;先加工精度较低的部位,后加工精度较高的部位;先加工平面,后加工孔。
4)先内后外原则
对于精密套筒,其外圆与孔的同轴度要求较高,一般采用先孔后外圆的原则,即先以外圆作为定位基准加工孔,再以精度较高的孔作为定位基准加工外圆,这样可以保证外圆和孔之间具有较高的同轴度要求,而且使用的夹具结构也很简单。
5)减少换刀次数的原则
在cnc加工中,应尽可能按刀具进入加工位置的顺序安排加工顺序。
在深圳诺铂智造看来,要提高cnc加工效率,要从观念转变、人才培训、工艺改进、柔性制造、设备维护和综合配套管理几个方面进行,具体如何有效提高cnc加工的效率与品质?应从以下几方面做起:
一、编程技巧
数控编程是cnc加工最基础的工作,工件加工程序编制的优劣直接影响机床最终的加工精度和加工效率。可以从巧妙的使用固有程序、减少数控系统的累积误差、灵活运用主程序和子程序等几个方面入手。
1、灵活运用主程序与子程序
进行复杂模具加工中,一般采用一模多件的形式进行加工。如果模具上有几处相同的形状,应灵活运用主程序与子程序的关系,在主程序中反复调用子程序,直到完成加工。不仅可以确保加工尺寸的一致性还可以提高其加工效率。
2、减少数控系统的累积误差
一般使用增量方式进行工件的编程,是以前一点为基准进行加工的,这样连续执行多段程序必然产生一定累积误差,所以在程序编制时尽量使用绝对方式进行编程,使每个程序段都以工件原点为基准,这样就能减少数控系统的累积误差,保证加工精度。
加工精度主要用于生产产品程度,加工精度与加工误差都是评价加工表面几何参数的术语。但任何加工方法所得到的实际参数都不会绝对准确,从零件的功能看,只要加工误差在零件图要求的公差范围内,就认为保证了加工精度。
机械加工精度是指零件加工后的实际几何参数(尺寸、形状和位置)与理想几何参数相符合的程度。它们之间的差异称为加工误差。加工误差的大小反映了加工精度的高低。误差越大加工精度越低,误差越小加工精度越高。下面简单介绍下提高工件加工精度的方法有哪些:
一、对工艺系统进行调整
(1)试切法调整通过试切-测量尺寸-调整刀具的吃刀量-走刀切削-再试切,如此反复直至达到所需尺寸。此法生产效率低,主要用于单件小批生产。
(2)调整法通过预先调整好机床、夹具、工件和刀具的相对位置获得所需尺寸。此法生产率高,主要用于大批大量生产。
二、减小机床误差
(1)应提高轴承的回转精度:①选用高精度的滚动轴承;②采用高精度的多油锲动压轴承;③采用高精度的静压轴承
(2)提高与轴承相配件的精度:①提高箱体支撑孔、主轴轴颈的加工精度;②提高与轴承相配合表面的加工精度;③测量及调节相应件的径向跳动范围,使误差补偿或相抵消。(3)对滚动轴承适当预紧:①可消除间隙;②增加轴承刚度;③均化滚动体误差。
(4)使主轴回转精度不反映到工件上

三、减少传动链传动误差
(1)传动件数少,传动链短,传动精度高;
(2)采用降速传动是保证传动精度的重要原则,且越接近末端的传动副,其传动比应越小;
(3)末端件精度应高于其他传动件。
四、减小刀具磨损
(1)在刀具尺寸磨损达到急剧磨损阶段前就必须重新磨刀
(2)选用专用的切削油进行充分润滑
(3)刀具材质应当符合工艺要求
五、减小工艺系统的受力变形
(1)提高系统的刚度,特别是提高工艺系统中薄弱环节的刚度;
(2)减小载荷及其变化
六、减小工艺系统热变形
(1)减少热源的发热和隔离热源
(2)均衡温度场
(3)采用合理的机床部件结构及装配基准
(4)加速达到传热平衡
(5)控制环境温度
七、减少残余应力
(1)增加消除内应力的热处理工序;
(2)合理安排工艺过程。
以上就是加工工件减少误差的方法,合理安排工艺可以有效提高工件的精度。
二、合理的设置加工路线
合理的设置加工路线和加工顺序是优化工件加工程序编制的重要基础。可以从加工轨迹方面和进刀方式方面加以考虑。在进行工件数控铣削加工时,要结合工件的工艺性要求去选择合适的进刀方式,以确保工件的切削加工精度和加工效率。在铣削平面工件外轮廓时,应安排好刀具的切入、切出路线。尽量沿轮廓曲线的延长线切入、切出,以免交接处出现刀痕。同时在铣削加工中应根据工件情况选择顺铣还是逆铣
三、刀具的选择和正确安装
不论是cnc加工还是普通加工,刀具因是直接作用于工件的,所以它的选择和安装时工件加工精度和表面质量最主要的因素。特别是工件在cnc加工中心上加工,刀具事先都储存在刀库中,一旦开始加工不得随意更换。所以刀具选择总的原则是:安装调整方便、刚性好、耐用度和精度高等。
四、切削用量的合理选择:
切削用量的确定是cnc加工工艺的重要内容,它的大小是机床主运动和进给运动的重要参数,对工件加工精度、加工效率以及刀具磨损有着重要的影响。切削用量的选择包括切削速度、背吃刀量以及进给量。基本的选择原则是:在刚度允许的条件下,粗加工取较大的切削深度,以减少走刀次数,提高工件生产率;精加工一般取较小的切削深度,以获得较高的表面质量。
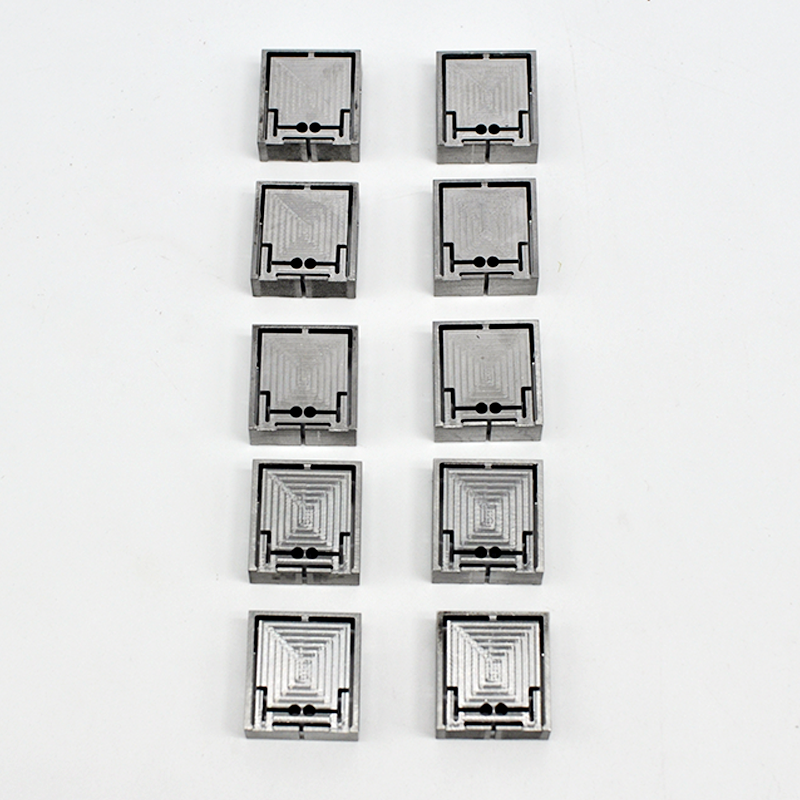
随着社会对产品多样化、制造低成本、制造周期短的要求日趋迫切,由于微电子技术、计算机技术、通讯技术、机械与控制技术的进步,柔性制造技术发展迅猛并且日臻成熟。cnc加工采用先进的刀具和机床实现高速,高效的切削,同时采用相关技术和管理方法优化整个CNC加工工艺,采用多种方式提高加工效率,实现高速切削、高效切削,高效加工,最终目标。